ATACC
INSTALLATION AND USE (05/12/02)
Safety Considerations Gasoline
is flammable and explosive. Do not smoke or allow open flames or sparks near
areas where gasoline is used. If you get gasoline in your eyes swallow gasoline,
get immediate medical attention. If you spill gasoline on your skin or clothing,
wash immediately with soap and water and change clothing. Never run the engine
an enclosed area. Exhaust fumes are poisonous and can result in loss of consciousness
and death in a short time. When drilling , wear safety glasses. Do not
drill where sparks can reach gasoline. To avoid injury, always check free
throttle operation before starting engine. THIS PRODUCT IS NOT FOR AIRCRAFT
USE.
WARNING: Installation and use of this regulator requires mechanical
and carburetor tuning skills, and may result in engine damage caused by decreased
fuel delivery. For information on carburetor tuning see Aaen’s “Carb Tuning
Handbook” (262) 552-8981. We are unable to verify every application
and installation of this product; verify proper fuel flow using EGT, piston,
and/or plug readings. This is your responsibility. KEEP THESE INSTRUCTIONS;
give to the sled’s new owner when selling.
Principle
of Operation This carburetor
compensator decreases fuel flow by applying a regulated vacuum to the float
bowls.
INSTALLATION
1.
Determine Your Existing Carb Venting Method Three factory vent locations are: air box, under-hood,
or handlebar. Most Polaris, newer Ski-Doo and some earlier Mach Z, and Yamaha
Viper have carbs vented in the air box. Most other sleds have under-hood
venting (vent lines hung down beneath the carbs). (Note: Some Arctic
Cat’s have enrichment circuit air tubes run to the air box; these are not
vent tubes). Some mid-90’s Polaris’ had the carbs vented to the handlebar.
2.
Check/ Change Carb Jetting Jet your carbs for -20F (-29C) and the
lowest altitude at which you ride. If you ride at temperatures lower than
-20F (-29C), then jet your carbs for -40F (-40C) and the lowest altitude
at which you ride.
3.
Install the Vacuum Source per attached sheet. After installation and always
before starting engine verify free throttle movement.
4.
Install the Compensator: For most applications, the best location for
the compensator is in the air box. Other locations will work, such
as behind or above the air box, but these locations must never have temperatures
significantly above the temperature inside the air box. If you do not have
an air box, locate the compensator as far as possible from engine/ exhaust
heat. If installing in the air box, drill a 9/16” hole in any location allowing
easy access; a good location is in the upper portion of the box on the clutch
side facing the engine. For example, on a 2002 600 EDGE, a good location
was in the lower portion of the box in the white plastic near the clutch side
wall. On a 2002 700 MXZ, a good location was in the front wall 1 5/8” from
the clutch side wall and down 1 1/4” from the top of the box. The inlet wire
screen and plastic inlet insert were removed eliminating the need to separate
the two box halves. Insert the outlet end of the compensator into
this 9/16” hole from the inside of the box, and secure with an approximately
1.75” piece of 1/2” i.d. tubing and a clamp. This results in most of the compensator
being inside the box with about .5” of the outlet end outside the box. See
schematic. For drainage, rotate so the side fitting slopes slightly downward
from the compensator.
5.
Install the Vent The vent
(air intake) is the 5/8” black fitting coming off the side of the compensator.
This fitting may be rotated to any desired orientation but downward is preferred.
This vent fitting should be vented to a location similar to the factory
location determined in 1. above using any length up to that supplied
of 1/2” i.d. inlet tubing. The inlet tube should not be crimped or restricted;
this will cause the engine to run lean. An elbow for 1/2” o.d.
(3/8” trade size) copper tubing (only) may be used for tight bends.
5a. Air Box Venting: If you have
air box venting, vent in the air box in the same compartment as the factory
vents. Attach the foam inlet filter directly to the black 5/8” fitting,
or 1/2” i.d. tubing may be used to move the vent to the desired location.
It is not necessary to cap the factory vent tube barbs on the air box.
5b. Under-Hood or Handlebar Venting: If
you have under-hood or handlebar venting, vent outside (not in) the
air box. CHANGING FROM UNDER-HOOD OR HANDLEBAR VENTING TO AIR BOX VENTING
WILL CAUSE A LEANING OF THE FUEL MIXTURE AND POSSIBLY ENGINE DAMAGE.
Use 1/2” i.d. tubing to vent to a suitable location outside the air box
which is not exposed to excessive engine or exhaust heat or snow or belt dust.
Attach the foam filter over the end of the 1/2” i.d. vent tube
6.
Outlet Install the reducer fitting into the 1/2” i.d. tubing
which you placed on the outlet end of the compensator in 4. above placing
it at least 3/8” from the end of the plastic screw head. Two reducer fittings
are supplied; the longer reducer fitting will reduce fuel flow less aggressively
as altitude increases and should be installed initially. Connect the
reducer fitting to the vacuum source using 24-28” of 1/4” i.d. tubing
(outlet tube length affects operation). See vacuum source instructions
for outlet tubing for late model Ski-Doo.
7.
Install Float Bowl Lines (5/32” i.d. tubing) using the schematic as a guide.
The entire system must be leak-free. Flooding or extreme riding can result
in fuel in the float bowl lines; tube routing should always be uphill
from the carbs enabling complete drainage of the lines. Any fuel
in the lines will result in erratic operation. In cases of extreme riding,
one-way valves from Holtzman Engineering, Inc. (only) can be placed
at each carb float bowl (overflow) fitting. For carbs with only one float
bowl fitting, simply join the fittings with a tee or 4-way connector. Rarely
carbs have an overflow standpipe drain; if present it must be sealed or connected
to a one-way valve from Holtzman Engineering, Inc. (only). If your
float bowl fittings are too small to seal to the 5/32” tubing, these fittings
may be “bushed out” using the red tubing supplied, or you may use 1/8”
i.d.
tubing if desired.
8.
Install the Control Chamber in the air box in a location preferably lower than the
compensator which allows connection to the compensator using all of
the 1/16” i.d. tubing supplied.
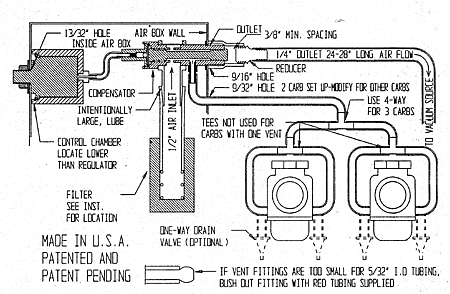
TUNING AND USE
09.
Initial Set Screw Setting There is a set screw located in the compensator which
may be rotated by inserting the .050” hex key supplied through the brass 1/16”
hose barb. Each clockwise 1/6 turn (1 flat of the hex) of the set
screw causes the ATACC to lean an additional 2%; counterclockwise
rotation has the opposite affect. If you are jetted for -20F (-29C) (see
2. above), leave the set screw at the factory position. If you are
jetted for -40F (-40C) initially rotate the screw 1/6 turn (1 flat) clockwise.
If you are jetted for 0F turn the set screw 1/6 turn (1 flat) counterclockwise.
Rotation of the plastic screw at the outlet end of the ATACC
has no affect on operation of the ATACC (it does not work like
a TEMPA FLOW screw) and should not intentionally be rotated.
10.
Initial Pressure Setting of the Control Chamber
is accomplished by simply removing and re-attaching one end of the 1/16”
i.d.
tube which connects the compensator to the control chamber. THIS SHOULD
BE DONE AT YOUR JETTED (LOWEST) ALTITUDE and may be done at any temperature.
11.
Proper Fuel Flow Verification With the set screw set per 09. above, run the
engine at several throttle positions and at your lowest altitude and the lowest
temperature possible. Adjust carb jetting if necessary. Then increase your
altitude, and if the fuel flow does not reduce fast enough as altitude increases,
remove the long reducer fitting and install the short one.
12.
Warm Drive-Away For the first mile (longer if the body is not
in the air box) after moving from warm storage or stopping for a break, do
not run the engine at extended high load but occasionally vary the throttle
position.
LIMITED
WARRANTY The installation of this device requires mechanical
and carburetor tuning skill. Because of the custom nature and the limitless
application variables this product is subject to, this product is sold with
a limited warranty only. Holtzman Engineering, Inc. makes no warranty of any
kind except we will replace this product if found to be defective in material
or workmanship for one year from date of purchase. Holtzman Engineering, Inc.
will not be held liable for any injuries or damages incurred as a result of
the installation or use of this product nor the parts this product may affect.
|